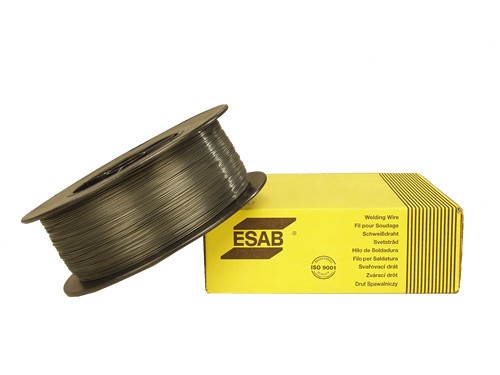
ESAB Dual Shield II 110 Flux Cored (FCAW) Welding Wire
Category
Low Alloy / High Strength
Manufacturer ESAB
Description
Dual Shield II 110 is an all-position flux cored electrode which produces a smooth spray-like transfer, low spatter levels, low diffusible hydrogen levels, easy slag removal and good arc direction. Dual Shield II 110 was designed to join high strength steel such as HY-100 and T-1 (25.4) in the as welded or stress relieved condition using 75% Ar / 25% CO2 shielding gas. It is well suited for joining high tensile steels that will be used in low temperatures. The weld metal analysis is similar to an E11018-M low hydrogen electrode.
Features
- ESAB pioneered the development of gas-shielded flux-cored welding (FCAW) in 1957. Today, ESAB offers the broadest variety of mild steel and low alloy flux-cored wires available anywhere in the world.
- ESAB cored wires offer flat welds with deep penetration and wetting into plate, with high deposition rates and efficiencies. This dramatically reduces weld time, increasing productivity.
- Flux-cored welding can be up to three times more productive than Stick and up to 2.5 times more productive than MIG. FCAW also offers productive positional welding and low diffusible hydrogen levels (H5) when required.
- ESAB Coreweld metal-cored wires were developed to meet the needs of demanding applications, such as structural steel construction, heavy equipment, transportation, bridges, petrochemical processing, offshore rigs, railcars, shipbuilding, pressure vessels, and general fabrication.
- Utilizing advanced manufacturing processes and specially formulated composite fillers, Coreweld metal-cored wires combine high deposition rates and efficiencies, high travel speeds, excellent penetration, and ease of use. Metal-cored wires also provide excellent arc stability and outstanding penetration and wetting, with superior fusion at the root joint and sidewall. The result is a high-quality weld with minimal slag and spatter, and fewer residual silica islands.
- Metal-cored wires offer several advantages over solid wire. Since metal-cored wires carry the current on the outer sheath, current densities are considerably higher than those found in wires sold, where the current is carried across the entire cross-sectional area. As a result, the metal-cored arc tends to be softer and can bridge gaps easier with reduced tendancy for burn through.
Specifications
Category
Low Alloy / High Strength
selection not available, try a different combination
selection not available, try a different combination
Call for price